Case Study: How Atlas® Supports Best Value for Store Remodeling
Case Study: How Atlas® Supports Best Value for Store Remodeling
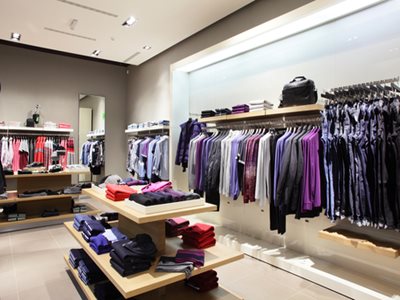
Major Roles
The Customer. Represents the retailer who requests logistics services.Material Suppliers. Manufacturers who provide construction materials, fixtures, and furnishings.
Atlas Logistics TM Account Coordinator. Key contact at Atlas ® HQ who oversees the logistics plan of the project, and provides operational support to all parties throughout the process.
Customer Field Contact. Project manager representing the customer who manages the on-site construction crew and works closely with the Atlas ® Agent for delivery of materials and assistance as needed.
Atlas ® Agent. The Atlas ® Agent is responsible for the direct transportation, handling of materials and managing labor crews as directed by Atlas Logistics TM.
***
The Optimal Warehouse Location

Once the warehouse location is determined, the Atlas ® Agent does a site survey of the store location. Any special considerations for delivery, such as restricted access, extended carries, or security concerns, are factored into the service plan.
Locating the warehouse within 50 miles of the job site is usually ideal. Atlas LogisticsTM also serves remote locations, orchestrating deliveries from four or more hours away.
Gathering the Goods
Four weeks prior to construction, the Atlas ® Account Coordinator schedules transportation of goods with the Material Suppliers. Atlas ® trucks pick up materials at each provider’s location and delivers to the project warehouse. In total, inbound goods shipments average about ten truckloads and about eight partial truckloads loads ( LTL). The Atlas warehouse secures all materials for the project a full seven days before construction begins.Managing the Inventory
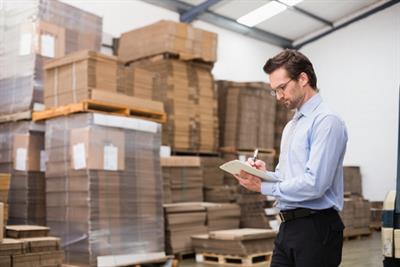
Working After Hours
Construction spans four to twelve weeks, depending on the store size, and extent of remodeling. Since stores stay in operation during remodeling, deliveries take place after the close of business.During the course of construction, the Atlas ® crew will perform 20 to 30 deliveries of fixtures: lighting, flooring, case goods, cash wraps, etc. They ensure all materials stay safe from damage throughout transit, using pad-wrapping as the primary means of protection. The onsite construction crew handles the unloading, with Atlas ® personnel assisting as requested by the Customer Field Contact. As always, teamwork is the guiding principle.
Atlas® provides delivery of rooftop HVAC units via flatbed truck. The units may weigh 2000 pounds or more. The Customer Field Contact provides the crane and rigging for off-loading and rooftop placement.
Finishing with Inside Placement and Reverse Logistics
After all permanent fixtures are installed the stage is set for completion. Atlas ® makes the final delivery of furnishings, tables, racks, and mannequins typically on a Sunday night. This is the most labor-intensive task in the process. It requires five to seven truckloads and an Atlas ® crew of 12 to 25 men. At the Store Manager’s direction, the Atlas ® crew will ensure all items are placed appropriately inside. They will remove and recycle any debris, such as the packing used for mannequins.The project concludes with a reverse logistics solution. The Atlas ® crew loads designated items from within the store and takes them back to the warehouse. The Atlas ® agent then dispatches the items as instructed for reuse at other stores, return to the manufacturer, or recycling. If items are designated for use in another store, Atlas Logistics TM will deliver those within seven days.